Groen is weer een hippe kleur bij machines
Sustainability rode draad Tijdens EMO hannover
Als er één thema was dat bij bijna alle machinebouwers op de EMO Hannover eerder dit jaar aan bod kwam, dan is het 'sustainability'. Iedereen presenteerde oplossingen om met de machines minder energie te verbruiken ergo minder CO2 uit te stoten. Is dit echt de oplossing voor een duurzame maakindustrie?
Sustainability
Groen is weer een hippe kleur in de werktuigmachinebouw. Niet letterlijk, maar in overdrachtelijke zin. De sector deed op de EMO Hannover z’n best om een groen imago uit te stralen. Vrijwel alle fabrikanten presenteerden hun ideeën en oplossingen om de maakindustrie aan te zetten tot energiebesparing en tot het reduceren van de uitstoot van broeikasgassen.
De sector voelt zich daartoe verplicht. Energie-efficiëntie en circulaire economie zijn twee thema’s waarmee de maakindustrie aan de slag moet. Tegelijk wordt er op gewezen dat productietechnologie vooral een enabler is voor de groene transities in de samenleving. Martin Welcker, commissaris van de EMO Hannover, vatte het zo samen: "Productietechnologie is geen insider business, maar het antwoord op de problemen van deze tijd."
Waar komt die aandacht vandaan?
Deze trend richting sustainability komt niet zomaar uit de lucht gevallen. Naast de ESG-criteria (Environment, Social en Governance - criteria om de impact van een bedrijf op het milieu, de ethische impact en die op de samenleving te meten) uit de financiële wereld is met name de CSRD-regelgeving een aanjager van de drang naar meer duurzame oplossingen. De E.U. wil naar net-zero: per saldo geen CO2-emissie meer.
Deze CSRD-richtlijn (Corporate Sustainability Reporting Directive) verplicht de grootste bedrijven vanaf 2024 om over hun milieu-impact en de broeikasgasemissies te rapporteren, inclusief de Scope 3-emissies, de indirecte emissies in de waardeketen. Dit betreft met andere woorden de uitstoot in zowel de toeleverende industrie als die bij de gebruikers van de producten, in dit geval de werktuigmachines.
Grote bedrijven zullen aankloppen bij hun toeleveranciers om data over onder andere de CO2-emissie bij de productie van componenten op te vragen. "Maar ook kleinere maakbedrijven krijgen hiermee te maken", zo waarschuwde de nieuwe VDW-voorzitter Markus Heering in de aanloop naar de EMO. "Duurzaamheid wordt gestuurd door wettelijke regelgeving. Ook de kleinere spelers in de producerende industrie moeten hier aandacht aan besteden. Als grote bedrijven vanaf 2024 verplicht hun CO2-footprint moeten rapporteren, dan heb je oplossingen in de hele productieketen nodig. De CO2-footprint van de industrie moet duurzamer worden."
Agoria heeft voor België berekend dat de industrie verantwoordelijk is voor 29% van alle CO2-uitstoot. Hieraan dragen de procesindustrie, chemie, metaal en cement het meeste bij. Volgens Agoria kan de maakindustrie de CO2-uitstoot terugdringen met 10 tot 12,3% tegen 2030 door robotisering, proactief onderhoud en digitalisering, zoals het gebruik van digital twins.
Duurzaamheid wordt gestuurd door wettelijke regelgeving. Grote bedrijven worden al verplicht hun milieu-impact te rapporteren, maar ook kleinere maakbedrijven zullen hier aandacht aan moeten besteden
Energie besparen uit kostenoogpunt
Soms denken we dat Europa voorop loopt als het om energiebesparing gaat. In Japan is dit onderwerp echter al veel meer geaccepteerd, wist een Japanse machinebouwer ons tijdens de EMO in Hannover te vertellen. Ze presenteerden er hun nieuwste OSP P500-besturing, met verschillende features om energie te monitoren, het verbruik te optimaliseren en CO2-emissies te registreren.
In Japan komt de interesse voor energiebesparing met name voort uit de hoge energieprijzen. In Europa is een dergelijke trend pas in recente jaren komen opzetten. Verschillende machinebouwers zien dus volop kansen om met minder energie toch dezelfde productie te draaien.
De quick win is goed kijken naar de randapparatuur in een CNC-bewerkingscentrum, bv. de installatie voor afzuiging van olienevel. Die kan soms best uit. De grootste besparing zit in het bewust inschakelen van de pompen die het koelsmeermiddel rondpompen. Onder de noemer Green Smart Machines wil de Japanse machinebouwer in de komende jaren nog meer features via de software aanbieden.
De maakindustrie kan de CO2-uitstoot terugdringen met 12,3% door robotisering, proactief onderhoud en digitalisering
Dynamische koeldrukregeling en AI
Met dynamische koeldrukregeling, Adaptive Coolant Flow is hoe een Duitse machinefabrikant de oplossing hiervoor noemt, is een concept dat meerdere fabrikanten aanbieden. De hoeveelheid koelsmeermiddel die wordt rondgepompt wordt aangepast aan de bewerking.
Wetenschappers van het Institut für Fertigungstechnik und Werkzeugmaschinen (IFW) van de Leibniz Universität Hannover hebben voor de ontwikkelaar van hyperMill CAM-software onderzocht hoe groot het besparingspotentieel is. Een dynamische koeldrukregeling kan tot 33% energie besparen bij het frezen van een blok titanium, zonder dat de productiviteit of de standtijd van de gereedschappen hierdoor negatief beïnvloed worden. De softwareontwikkelaar overweegt deze strategie te integreren in de CAM-software. De 33% betreft het energieverbruik voor het koelsmeren.
Een machinefabrikant uit Duitsland denkt dat je best 30% kunt besparen op het totale energieverbruik. "We laten hier op de EMO Hannover zien hoe je met twaalf maatregelen op een DMU 65 monoBlock tot zo’n 18.000 kWh per jaar aan energie kunt besparen."
Recycling van alle materialen en het minimaliseren van de bewerking worden belangrijker
Recuperatie van energie bij het afremmen van de assen is één van die oplossingen; kortere opwarmcyclus leveren 16% op; het energieverbruik in de stand-bymodus kan bijna gehalveerd worden en de grootste besparing komt uit het in- en uitschakelen van het koelsmeersysteem op de machine.
Maar de Duitse machinebouwer bedacht nog een andere creatieve oplossing om energie te besparen. Zeker in de onbemande productie is het wegspoelen van spanen cruciaal. Liever te veel spoelen dan te weinig. Maar dat kost energie. Het bedrijf zet daarom Artificiële Intelligentie in: via beeldherkenning wordt gezien waar nog spanen liggen en via de gestuurde nozzles kan men deze gericht wegspoelen.
Stand-bymodus
Een andere machinebouwer uit Japan gaat onder het label Neo een nieuwe lijn machines lanceren, geoptimaliseerd voor een minimaal energieverbruik en gecombineerd met korte bewerkingscycli. Ook zij schermen met een flinke energiebesparing (van 30%), wat ze demonstreerden op een Variaxis i-700 Neo. Daarnaast zit er in de stand-bymodus van de machine nog een groot besparingspotentieel. Vergeleken met een gelijkaardige machine uit 2010 spreekt het bedrijf over een 46% lager energieverbruik in de stand-bymodus.
De rol van multitasking en digital twins
Als je de doorlooptijd verkort, bespaar je eveneens. Multitasking is de oplossing hiervoor. En je hebt minder medewerkers nodig, wat in de wereldwijde krappe arbeidsmarkt misschien nog wel belangrijker is. Nauwkeurigheid en stabiliteit zijn dan wel een vereiste. Zorgen voor minder afgekeurde producten draagt direct bij aan het verbeteren van de milieu-efficiency.
Op EMO Hannover 2023 demonstreerde het Institut für Fertigungstechnik und Werkzeugmaschinen (IFW) van de Leibniz Universität Hannover ook een zelflerende machine. Via artificiële intelligentie voorspelt de digital twin van de machine eventuele vormafwijkingen al vóór de eigenlijke bewerking en past het programma aan. Ook worden eventuele fouten in real time herkend en direct hersteld. Dit alles moet leiden tot minder afgekeurde producten, en dus minder materiaal- en energieverspilling.
Duurzaam met gereedschappen
Niet alleen de machinebouwers grepen het thema sustainability met beide handen aan, ook gereedschapsfabrikanten zijn hier op verschillende manieren mee bezig.
Een fabrikant uit Frankrijk, gespecialiseerd in Powder Metallurgy Steels en High Speed Steels, heeft bijvoorbeeld als eerste een lijn HSS-gereedschappen gelanceerd die volledig gemaakt zijn van gerecycleerd metaal.
Een Luxemburgse fabrikant van gereedschappen lanceerde de Product Carbon Footprint Standard (PCF) voor hardmetalen gereedschappen. Het bedrijf gaat deze PCF-standaard voor elk product bij elke rekening voegen, zodat de klanten gemakkelijker hun eigen CO2-voetafdruk van een bewerking kunnen berekenen. Daarnaast kan men deze waarden benutten om een strategie te ontwikkelen hoe de eigen CO2-emissie terug te dringen. Aan de letter, die voor een bepaalde emissieklasse staat, ziet men in één oogopslag welk gereedschap een kleinere CO2-voetafdruk heeft. Ook wordt een gemiddelde CO2-emissie per kilogram product dat men bewerkt meegegeven. De gereedschappen uit de upGrade-lijn, die volledig van gerecycleerd hardmetaal zijn gemaakt, hebben de kleinste CO2-voetafdruk. De berekeningsmethodiek van de Luxemburgse fabrikant voldoet aan de norm ISO 14067.2018 en is beoordeeld door een externe partij.
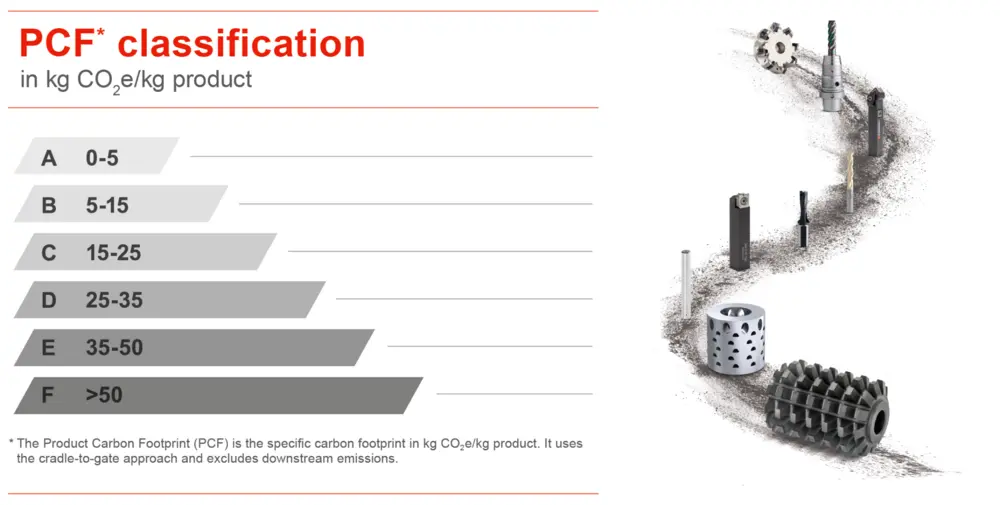
Zelfs als men de emissies die bij bewerkingen vrijkomen volledig tot nul zou kunnen reduceren - wat natuurlijk een utopie is - dan blijft nog steeds de helft van het Global Warming Potential over
Het materiaal is de boosdoener
Zal dit alles de verspaning helpen om de CO2-voetafdruk te verkleinen? Ongetwijfeld. Minder energieverbruik omdat een pomp niet meer standaard altijd meedraait, scheelt meteen energie en dus CO2-emissie. Beter kan men de vraag stellen of hiermee de verspanende industrie naar een net-zerosituatie kan gaan.
Het antwoord op die vraag werd al enige tijd geleden gegeven door het Fraunhofer IPT in Aken. Dat heeft een Life Cycle Impact Assessment uitgevoerd voor het frezen van een vliegtuigonderdeel gemaakt uit titanium en een gemaakt uit nikkel. Zowat de helft van de Global Warming Potential zit in het materiaal, zo blijkt daaruit. GWP is een internationale maatstaf voor de bijdrage aan de opwarming van de aarde. Voor titanium is dit ruim 49%. Bij nikkel is dit meer dan 45%. Met andere woorden: zelfs als men de emissies die bij de bewerking vrijkomen volledig tot nul zou kunnen reduceren – wat natuurlijk een utopie is – dan blijft nog ongeveer de helft van de GWP-waarde over.
Zo’n 30% van de bijdrage aan de opwarming van het klimaat zit in het verspaningsproces; daarvan neemt het hardmetalen gereedschap volgens de onderzoekers zo’n 10% voor zijn rekening. Recycling van hardmetalen gereedschappen zet dus qua klimaatdoelen wel degelijk zoden aan de dijk.
Minder onderdelen maken?
Eerder dit jaar kwam het thema duurzaam produceren ook aan bod tijdens het Aachener Werkzeug Koloquium van Fraunhofer IPT en het Werkzeugmaschinen Labor. Het was zelfs hét thema van het AWK’23. De conclusie hier was dat de circulaire economie onmisbaar zal zijn: onderdelen moeten vaker hergebruikt worden, een tweede leven krijgen, hetzij in dezelfde functie, hetzij in een andere.
Een van de hoogleraren gebruikte in Aken de term 'upgrade economie': het opwaarderen van versleten producten, zodat ze opnieuw ergens voor gebruikt kunnen worden. In Aken onderzoekt men bijvoorbeeld of afgesleten matrijzen efficiënt hersteld kunnen worden met 3D-metaalprinten. Of bijvoorbeeld de mogelijkheid om onderdelen van een matrijs, zoals hot runners, weer in een andere matrijs te kunnen inzetten. Alles gericht op het terugdringen van het gebruik van grondstoffen, want daarin zit het grootste besparingspotentieel.
Andersoortige machines?
Recycling van alle materialen en het minimaliseren van de bewerking worden dus belangrijker. Dit betekent ook de vraag durven stellen of je voor elke bewerking wel een grote massieve CNC-machine nodig hebt. Ook voor het bewerken van kleinere, zelfs microcomponenten? Zal de drang naar duurzaamheid in de industrie het pad effenen voor de kleine, micro-CNC-machines die weinig energie verbruiken, weinig koelsmeermiddel vereisen ...?
Een Duitse machinebouwer van precisiemachines heeft de CO2-voetafdruk voor zijn machines laten berekenen en vergeleken met die van een standaard 5-assig bewerkingscentrum. De minimachine heeft een vier keer kleinere voetafdruk, wat zich direct vertaalt in een beter score als het om de CO2-emissie van een bewerking gaat. Minder massa vraagt minder energie om assen te verplaatsen en spindels die met hoge toerentallen bewerken frezen met geringere krachten. Is dat de toekomst?